In the ever-evolving Original Equipment Manufacturing (OEM) realm, precision and quality of components like DC current shunts are not merely important but essential. These unassuming yet vital parts enable accurate current measurement, crucial for optimal functionality and safety across devices and machinery. However, integrating them seamlessly into your products requires a critical first step: partnering with the right DC current shunt manufacturer. Choosing the ideal supplier is pivotal for ensuring your components meet stringent standards and your products perform reliably.
This guide aims to help you navigate the process of recognizing your OEM requirements, choosing a manufacturer that meets your quality and innovation standards, and establishing a partnership beyond transactions. Whether an industry veteran or newcomer, understanding DC current shunts, their uses, and their impact on product performance is crucial. The guide covers the intricacies involved, providing clarity and insights for an informed decision-making process.
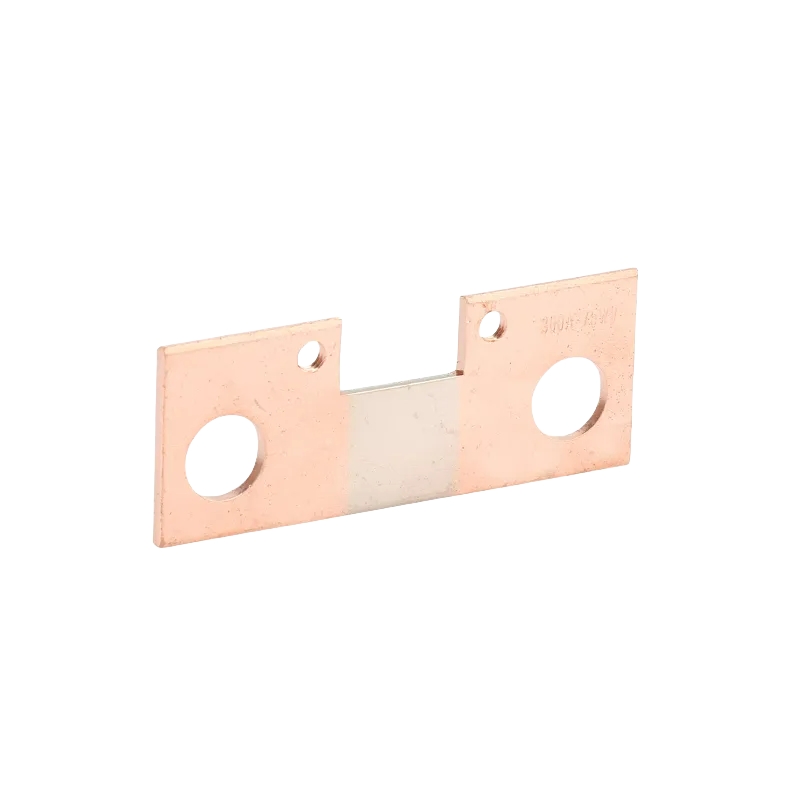
Finding the ideal OEM manufacturer involves evaluating your needs, considering selection factors, and nurturing a strong partnership. We’ll guide you through analyzing requirements, identifying criteria for choosing a partner, and fostering productive collaboration. Additionally, we’ll discuss potential hurdles and strategies to overcome them, ensuring your relationship remains resilient, efficient, and future-focused amidst technological advancements.
Discover the secrets to elevating your OEM projects with a reliable DC current shunt manufacturer. Embark on this insightful journey, where you’ll master the art of seamless collaboration, paving the way for groundbreaking innovations, unparalleled quality, and unmatched excellence within your industry pursuits.
Section 2: Understanding DC Current Shunts
2.1 What Are DC Current Shunts?
Current measurement in electronics relies on shunt resistors, called DC current shunts. These specialized resistors sense electrical current flow by detecting voltage changes across them. Industrial machines, cars, and gadgets all employ DC current shunts. Despite their simplicity, they provide a reliable technique for monitoring currents accurately.
2.2 The Role in Electrical Systems
Electrical circuits require precise monitoring to operate safely and efficiently. DC current shunts play a vital role by enabling accurate current measurements. These measurements are essential for controlling and protecting electrical systems, ensuring they operate within specified limits. By providing crucial data, current shunts contribute to the overall performance and dependability of electrical systems.
2.3 Types and Applications
Shunts for direct current come in various forms. Manganin shunts maintain steady performance across temperatures. Copper shunts work well with high currents. Choosing the suitable shunt depends on the specific application and requirements. Different shunts have distinct characteristics, so understanding these differences is crucial for making the right selection.
2.4 Impact on OEM Product Performance
Choosing an appropriate DC current shunt plays a crucial role in optimizing the functioning and dependability of OEM products. Selecting the suitable shunt facilitates precise current measurement. Moreover, it enhances the overall robustness and operational efficiency, directly impacting the market competitiveness and customer satisfaction with the product.
As we move forward, we’ll examine your unique requirements for DC current shunts from an OEM perspective. We’ll explore strategies to choose a suitable manufacturer and foster a collaborative relationship, ultimately enhancing the value and performance of your product.
Section 3: Identifying Your OEM Needs
3.1 Assessing OEM Needs for DC Current Shunts
Assessing your OEM needs is vital before partnering with a manufacturer. This entails comprehending the precise requirements for your application, such as the current measurement range, environmental conditions the shunt will face, and the requisite accuracy and stability standards. Some requirements may be complex, while others relatively straightforward, but all must be carefully evaluated.
3.2 Importance of Specifications, Performance, and Quality
Parameters like voltage drop, resistance value, and tolerance range are crucial to ensure the shunt meets your application’s needs. Factors such as long-term stability and response time directly influence the reliability and efficiency of your products. High-quality components help reduce failure risks and maintain your brand’s reputation. Short, straightforward sentences. Ensure component specifications align with application requirements. Performance characteristics impact product reliability and efficiency. High-quality parts minimize failures, preserve brand image.
3.3 Documenting Your Needs
A requirements document aids clear understanding between you and potential manufacturers. This guide outlines specifics like technical features, performance targets, quality benchmarks, and regulatory obligations. It acts as a core reference during production and testing phases, keeping everyone on the same page with your vision.
Identifying your Original Equipment Manufacturer (OEM) requirements is crucial. The subsequent step involves carefully selecting a manufacturing partner capable of satisfying those needs and upholding the essential standards for your products’ triumph.
Section 4: Choosing the Right DC Current Shunt Manufacturer
4.1 Criteria for Selecting a Manufacturer
The path forward lies in comprehending your OEM’s specific needs. Then, you must carefully navigate the selection process, identifying a manufacturer capable of meeting those requirements while upholding the necessary standards for your products’ triumph.
When evaluating DC current shunts, consider the manufacturer’s longevity in the field. A company with extensive industry expertise often demonstrates proficiency and dependability.
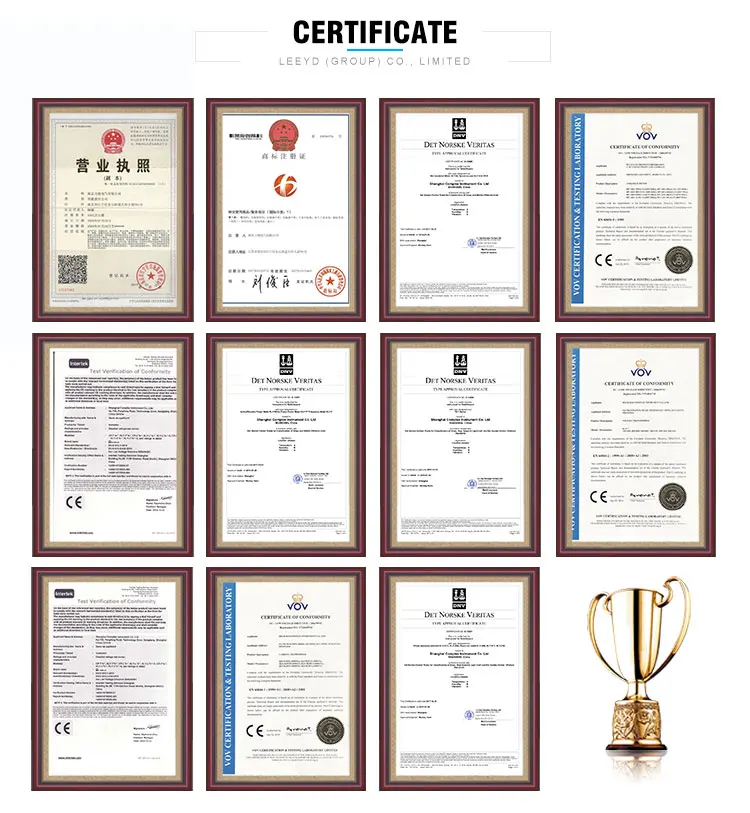
Verifying credentials is crucial – seek out accredited certifications like CE Rohs signifying dedication to quality assurance practices.
Ask manufacturers about their methods for ensuring consistent quality. Trustworthy products need dependable quality control protocols each step of the way.
4.2 Significance of Industry Reputation and Customer Testimonials
Industry reputation sheds light on a manufacturer’s dependability and quality benchmarks. Customers’ testimonials and case studies offer a window into other Original Equipment Manufacturers’ encounters and contentment with the supplier.
4.3 Verifying Manufacturer’s Expertise and Reliability
Consider visiting the facility before finalizing a partnership, if possible. Take a look at operations and quality control processes firsthand. You can request samples or run a pilot to assess capability meeting your needs properly.
Finding the ideal manufacturer is essential, as it lays the groundwork for a productive partnership that will impact the caliber and dependability of your OEM offerings. The subsequent section will delve into how to establish and nurture an effective collaboration with your selected manufacturing entity, fostering mutual achievement.
Section 5: Collaborating with Your Chosen Manufacturer
5.1 Establishing Effective Communication and Partnership
Clear interaction commences with building robust channels for exchange. Consistent gatherings, face-to-face or digital, may enable harmony regarding objectives, schedules, and outlooks. Open sharing of knowledge and critique proves pivotal for tackling obstacles promptly and nurturing faith between parties.
5.2 Engaging in Custom Design Processe
When your original equipment manufacturing requirements demand custom-designed shunts, active participation in the design process becomes crucial. This collaborative effort may involve reviewing design specifications, analyzing prototypes, and implementing necessary modifications based on testing outcomes to guarantee the final product aligns with your specific needs.
5.3 Prototyping and Testing
Prototyping is a critical stage where theoretical designs are transformed into tangible products. It allows you to evaluate the shunt’s performance in real-world conditions and identify any areas for improvement. Rigorous testing during this phase is crucial to ensure the product meets all specified criteria before moving into mass production.
5.4 Handling Logistics, Delivery Schedules, and Post-Delivery Support
Creating straightforward arrangements on transportation details and shipping timelines proves vital to prevent hitches in your manufacturing procedure. Additionally, determining a plan for assistance once the delivery arrives, encompassing potential methods for resolving any concerns or defects, demands equal significance.
The collaboration between you and your manufacturer extends beyond mere oversight of production. It involves forging a dynamic alliance capable of adapting to emerging needs and surmounting obstacles within your field. In the following section, we’ll explore strategies for addressing typical challenges that may surface during this collaborative journey, fostering a resilient and productive partnership.
Section 6: Conclusion
This comprehensive guide has explored the essential steps involved in collaborating with a reputable DC current shunt manufacturer. It underscores the significance of comprehending your OEM requirements, choosing the most suitable manufacturing partner, and establishing a robust collaborative framework. Ensuring adherence to quality standards, maintaining compliance, and staying up-to-date with industry advancements are vital factors that contribute to the success and longevity of your OEM products.
FAQ
1. When choosing a manufacturer for your OEM’s DC current shunt needs?
consider several factors. Look for companies with extensive industry experience and recognized certifications like CE, indicating robust quality control processes. Assess their reputation by examining customer testimonials and evaluating sample products or touring their facilities. Meeting these criteria can significantly enhance the quality and reliability of your final products.
2.To collaborate effectively with your selected DC current shunt manufacturer,?
establish clear communication channels from the outset. Actively participate in the custom design and prototyping phases, providing feedback and input. Scheduling regular check-ins and progress updates is also crucial. Aim for a partnership where both parties are open to feedback and aligned with project goals and expectations.
3.Collaborating with a DC current shunt manufacturer can present challenges like communication breakdowns, misaligned expectations, or supply chain disruptions?
Mitigate these by establishing regular communication protocols and clearly defining project scopes. Have contingency plans in place to address potential supply chain issues. Studying industry case studies or consulting with peers can offer valuable insights into effective collaboration strategies.
4.Staying informed about future trends and innovations in DC current shunt technology ?
Is essential to ensure your OEM products remain competitive and meet evolving market demands. Engage with your manufacturer to discuss integrating new technologies that can enhance your products’ performance and appeal, keeping you ahead in the industry.
5.What benefits can stem from prioritizing quality and compliance when collaborating with a DC current shunt supplier?
Upholding stringent quality standards and regulatory compliance ensures your products consistently deliver reliable, safe performance. This directly impacts your brand’s reputation and customer satisfaction levels. Fostering close cooperation with your manufacturer allows you to seamlessly integrate industry-accepted practices, rigorous quality assurance protocols, and continuous improvement processes. By proactively addressing quality concerns through frequent communication and monitoring mechanisms, you can maintain elevated product quality across all offerings.