In the labyrinth of electrical engineering, few components wield as much quiet influence as the DC shunt—a deceptively simple device engineered to master the invisible flow of electrons. Imagine a circuit where milliamp discrepancies could derail an entire system, or where thermal drift silently sabotages accuracy. This is the domain of the DC shunt: a meticulously crafted alloy core, often forged from manganin or constantan, designed not just to conduct, but to reveal. Unlike mundane resistors, shunts are the unsung sentinels of current measurement, blending ultra-low resistance with laser-cut stability to transform chaotic currents into quantifiable data.
What is a DC Shunt and How Does It Function?
In the heartbeat of electrical circuits—where currents surge and precision is non-negotiable—the DC shunt emerges as a masterstroke of engineering minimalism. Picture a device so unassuming it could be mistaken for a basic resistor, yet so pivotal it governs the accuracy of megawatt systems. At its core, a DC shunt is a high-precision current sensor, leveraging alloy alchemy and geometric wizardry to split electron flows without disrupting them. But its brilliance lies in the details: a labyrinth of manganin strips, terminal blocks engineered for zero thermal drift, and Kelvin connections that defy parasitic resistance.
What Components Make Up a DC Shunt?
Beneath its rugged exterior lies a symphony of materials. The shunt’s resistive element—often forged from manganin or constantan—is a metallurgical marvel, optimized for near-zero temperature coefficients. Precision-milled terminal blocks anchor the assembly, while electroplated surfaces combat corrosion. Even the solder joints are strategic, designed to minimize thermoelectric interference. This isn’t just hardware; it’s a marriage of material science and precision metrology.
How Does a DC Shunt Differ from a Regular Resistor?
Resistors resist; shunts reveal. While a standard resistor throttles current indiscriminately, a shunt operates as a silent collaborator, diverting a precise fraction of current to generate a voltage drop proportional to the flow. Its ultra-low resistance—often in the milliohm range—ensures minimal power loss, a stark contrast to the energy-wasting tendencies of conventional resistors. Here, resistance isn’t a bottleneck—it’s a calibrated gateway to measurement nirvana.
What Are the Key Specifications of a DC Shunt?
From current ratings that scale from microamps to kiloamps, to TCR (Temperature Coefficient of Resistance) values tighter than 10 ppm/°C, DC shunts are defined by their specs. Power dissipation limits, accuracy classes (think 0.1% or better), and frequency response thresholds form the trifecta of critical metrics. These aren’t just numbers—they’re the DNA of reliability in applications where a millivolt error could trigger catastrophic downtime.
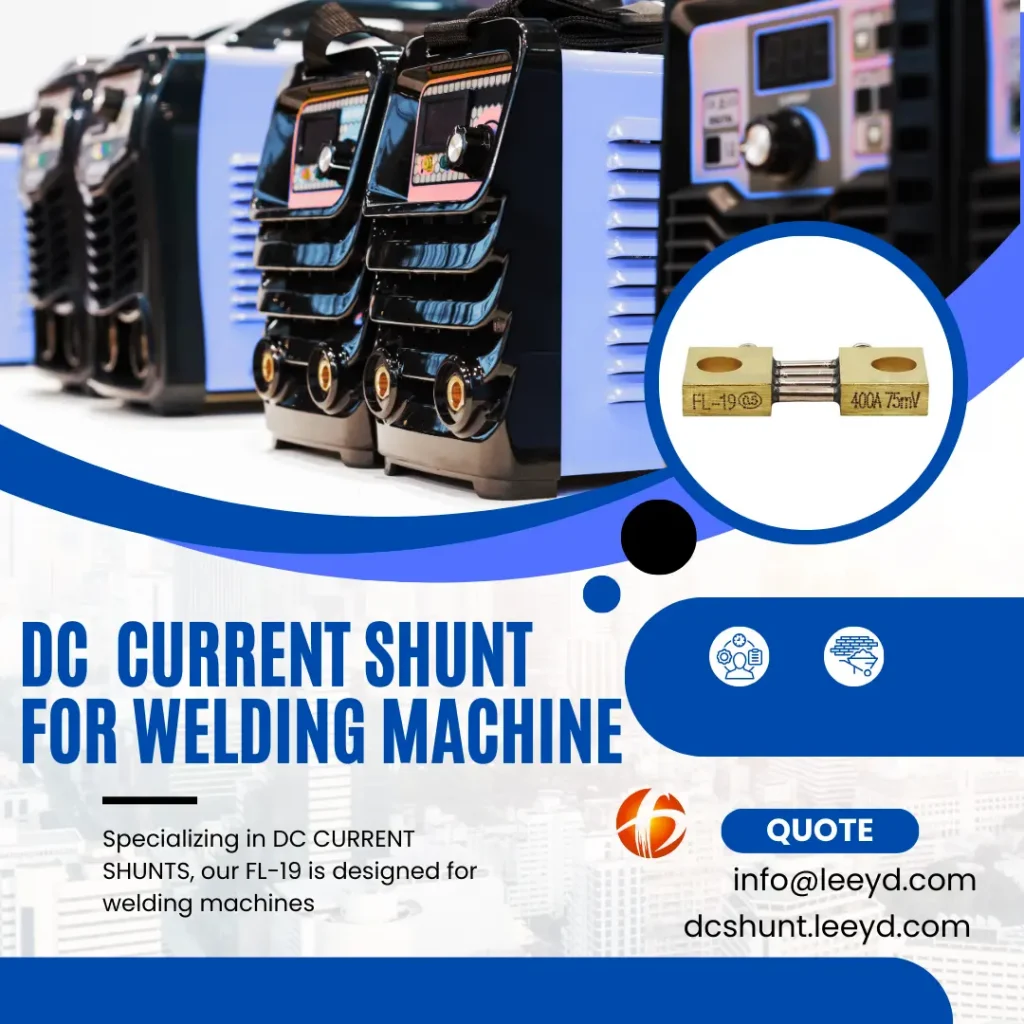
Why Are DC Shunts Critical in Electrical Systems?
In an era where energy efficiency and precision are non-negotiable, DC shunts stand as the unsung arbiters of electrical integrity. These unassuming components are the backbone of systems demanding flawless current measurement—from stabilizing microgrids to safeguarding EV battery arrays. But what elevates them from mere circuit elements to mission-critical assets? The answer lies in their ruthless efficiency, unyielding accuracy, and a design philosophy that treats milliohms like microns.
Why Do Engineers Prefer DC Shunts for Current Measurement?
Engineers don’t settle for approximations—they demand certainty. Unlike Hall effect sensors or current transformers, DC shunts offer a direct, analog truth-teller’s approach, converting current into voltage with unflinching linearity. Their passive design sidesteps electromagnetic interference pitfalls, while their scalability—from nanoamps to industrial kiloamperes—makes them the Swiss Army knife of metrology. In high-stakes environments like aerospace or medical imaging, where noise-free data is sacrosanct, shunts are the gold standard.
Why Are Low Resistance Values Essential in Shunt Design?
Low resistance isn’t a feature—it’s a mandate. A shunt’s milliohm-level impedance acts as a stealthy observer, siphoning off just enough current to measure without throttling the system. High resistance would spell disaster: parasitic power losses, thermal runaway, and skewed readings. By minimizing voltage drop, shunts preserve circuit efficiency while acting as silent sentinels, ensuring energy flows unimpeded even under load surges.
Why Is Accuracy Paramount in DC Shunt Applications?
In the realm of shunts, accuracy isn’t a luxury—it’s existential. A 0.1% deviation in a solar inverter’s current sensor could destabilize an entire power grid. A shunt’s alloy composition, Kelvin bonding, and TCR (Temperature Coefficient of Resistance) are engineered to combat drift, hysteresis, and thermal EMF—variables that turn lesser components into liabilities. This precision-first ethos is why shunts anchor life-critical systems, from defibrillators to nuclear reactor controls, where failure isn’t an option.
When Should You Use a DC Shunt in Your Circuit?
DC shunts are the silent guardians of circuits demanding uncompromising current visibility—but their deployment hinges on strategic intent. Deploy them when precision is non-negotiable, energy loss is intolerable, and the stakes of measurement drift could cascade into system-wide chaos. Whether optimizing a solar inverter’s efficiency or monitoring a submarine’s battery bank, shunts thrive where analog accuracy meets brutal environmental demands.
When Are DC Shunts More Effective Than Other Measurement Tools?
Choose shunts when electromagnetic interference (EMI) runs rampant, or when Hall effect sensors buckle under DC offset errors. In ultra-low current applications—think microamp leakage detection—or high-current industrial rigs (kiloamp smelting operations), shunts outclass alternatives with their passive, linear response. They’re the go-to in aerospace telemetry and lab-grade power supplies, where noise immunity and bandwidth limitations render active sensors obsolete.
When Should You Avoid Using a DC Shunt?
Bypass shunts in high-voltage systems where even milliohm drops could destabilize voltage rails, or in circuits allergic to parasitic power loss (e.g., energy-harvesting IoT devices). Avoid them where galvanic isolation is mandatory—shunts fuse the measurement circuit to the load, risking ground loops. Opt for current transformers or isolated sensors in AC-heavy or frequency-dynamic environments, where shunts’ inherent resistance becomes a liability.
When Do DC Shunts Require Calibration or Adjustment?
Calibrate shunts when thermal stress warps their alloy lattice, or when corrosion creeps into terminal junctions—common in marine or industrial settings. Post-installation, validate them after extreme current events (e.g., lightning strikes) that could anneal the resistive element. High-precision labs recalibrate biannually, but ruggedized shunts in EV charging stations might endure years untouched. Watch for drifting voltage drops or hysteresis in cyclic loads—these are the sirens of a shunt begging for recalibration.
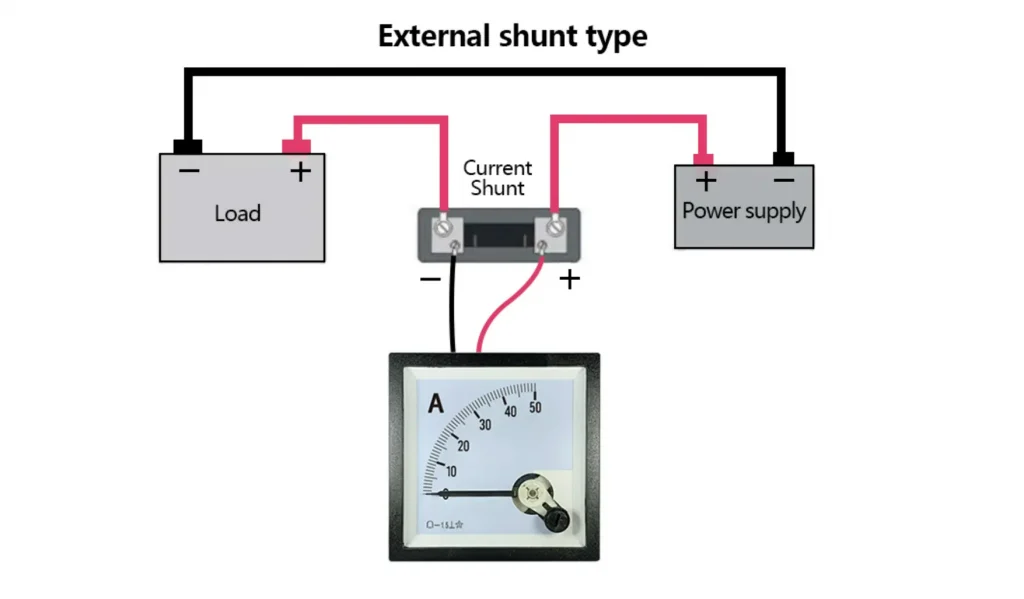
Where Are DC Shunts Commonly Deployed in Real-World Applications?
DC shunts operate in the shadows of modern infrastructure, their presence vital yet often overlooked. They anchor systems where current measurement is the difference between optimization and catastrophe—think smart grids balancing terawatts, or lab equipment dissecting nanowatt leaks. From subsea power cables to Mars rovers, shunts thrive in extremes, their rugged simplicity making them indispensable in environments too hostile for fragile electronics.
Where Do DC Shunts Play a Role in Automotive Systems?
In the electrified heartbeat of modern vehicles, shunts are the silent custodians of energy integrity. Embedded within EV battery packs, they monitor cell-level currents to prevent thermal runaway, while regenerative braking systems rely on shunts to precisely meter energy recapture. Even in internal combustion engines, shunts lurk in alternator circuits, ensuring voltage regulators maintain stable outputs—critical for preventing ECU (Engine Control Unit) malfunctions.
Where Are Shunts Used in Renewable Energy Installations?
Renewables demand ruthless efficiency, and shunts deliver. Solar arrays deploy them within combiner boxes to track string currents, flagging panel degradation before it cascades. Wind turbine converters use shunts to balance DC link currents, while grid-scale battery storage systems depend on their precision for state-of-charge calculations. Off-grid microgrids leverage shunts in bidirectional inverters, ensuring seamless transitions between solar, battery, and generator power—no flicker, no fail.
Where Do Industrial Machines Rely on DC Shunts?
Heavy industry is a gauntlet of extremes, and shunts are its unflinching sentinels. Electroplating tanks employ shunts to maintain exact current densities, depositing metal layers atom by atom. CNC machines embed them in servo drives to detect motor overloads before bearings melt, while arc furnaces use shunts to monitor megawatt currents without melting under the inferno. Even data centers, the silent giants of the digital age, rely on shunts in PDUs (Power Distribution Units) to prevent server racks from succumbing to voltage sag.
How Do DC Shunts Measure Electrical Current Accurately?
DC shunts are metrological maestros, transforming chaotic electron flows into quantifiable data through a ballet of physics and precision engineering. Their accuracy hinges on a trifecta of principles: immutable material properties, geometric exactitude, and environmental resilience. In a world where microvolts matter, shunts decode currents by embracing their role as passive observers—intercepting flows without interrupting them.
How Does Ohm’s Law Apply to DC Shunt Operation?
Ohm’s Law isn’t just a theory here—it’s the shunt’s DNA. By engineering a known resistance (R) into the device, the voltage drop (V) across its terminals becomes a direct proxy for current (I = V/R). But this isn’t basic arithmetic; it’s a high-stakes game where shunt alloys like manganin are tailored for near-zero TCR (Temperature Coefficient of Resistance), ensuring R remains rock-solid even as temperatures fluctuate. Every milliohm is a calculated constant, turning voltage into a current Rosetta Stone.
How Are Voltage Drops Converted into Current Readings?
The magic lies in calibration-grade instrumentation. Shunts generate microvolt-to-volt signals proportional to current, which precision amplifiers and ADCs (Analog-to-Digital Converters) amplify and digitize. Kelvin connections—four-terminal setups—bypass contact resistance, isolating the measurement path from parasitic losses. In high-current scenarios, even a 50 µV error could skew readings by amps, so shunts pair with instrumentation that treats noise like kryptonite.
How Do Environmental Factors Impact Shunt Accuracy?
Shunts wage war against entropy. Temperature swings induce resistance drift—combatted by alloys with ppm/°C stability. Vibration? It risks microfractures in the resistive element, demanding ruggedized designs. Humidity invites corrosion, countered by hermetically sealed terminals or gold plating. Even magnetic fields aren’t off the hook: shunts leverage non-magnetic materials to nullify inductive coupling. In aerospace or deep-sea applications, these factors aren’t nuisances—they’re existential threats meticulously neutralized.
What Are the Different Types of DC Shunts Available?
DC shunts are not one-size-fits-all; they’re engineered for niche demands. Beyond the basic fixed and adjustable variants, precision shunts dominate labs with 0.01% tolerance, while high-frequency shunts suppress parasitic inductance for switching power supplies. Temperature-compensated shunts combat thermal drift in harsh environments, and ultra-low-resistance models handle kiloampere surges in industrial rectifiers. Whether it’s a micro-ohm shunt for EV charging stations or a hermetically sealed unit for subsea robotics, diversity defines their DNA.
What Distinguishes Fixed vs. Adjustable DC Shunts?
Fixed shunts are the stoic sentinels—pre-calibrated with immutable resistance values, ideal for stable, repeatable measurements in grid-tied solar inverters or factory automation. Adjustable shunts, however, are the shape-shifters, featuring trimmer resistors or sliding contacts for on-the-fly recalibration. Think laboratory power supplies or legacy systems where aging components demand periodic tweaks. The trade-off? Fixed shunts prioritize rugged simplicity; adjustable ones sacrifice some durability for versatility.
What Materials Are Used to Build High-Performance Shunts?
The soul of a shunt lies in its alloy. Manganin (86% Cu, 12% Mn, 2% Ni) reigns supreme for its near-zero TCR (Temperature Coefficient of Resistance), while constantan tackles moderate currents with corrosion-resistant grit. For ultra-high stability, Evanohm® steps in, its nickel-chromium lattice defying thermal stress. Terminals often marry oxygen-free copper for minimal contact resistance, clad in gold or silver to repel oxidation. Even solder matters—cadmium-free alloys ensure micro-ohm stability under thermal cycling.
What Are the Differences Between High-Current and Low-Current Shunts?
High-current shunts are the bodybuilders of the family: thick manganin bars, water-cooled terminals, and milliohm resistances to handle 10kA+ without breaking a sweat. They’re built like radiators, prioritizing heat dissipation over compactness. Low-current shunts, conversely, are the watchmakers—delicate, precision-etched foils with resistances up to 1 ohm, optimized for microamp resolution. Their compact designs avoid thermal mass, relying on air cooling and TCR-optimized alloys. While high-current models anchor welding rigs and smelters, low-current cousins thrive in medical devices and photon counters.
How to Install and Calibrate a DC Shunt Properly?
Installing and calibrating a DC shunt isn’t just a task—it’s a ritual of precision. A misstep here could turn a $500 shunt into a liability, skewing data or melting under load. The process demands equal parts mechanical rigor and metrological finesse, blending torque specs with microvolt scrutiny.
How Do You Integrate a Shunt into an Electrical Circuit?
Integration starts with path purity. Position the shunt in series with the load, ensuring all current flows through its resistive element—no parallel sneak paths allowed. Use Kelvin (four-terminal) connections to isolate measurement leads from power terminals, bypassing contact resistance. Mounting matters: secure the shunt to a heat-sunk baseplate to combat thermal expansion, and avoid bending stresses that could fracture its alloy core. For high-current setups, bus bars must be torque-wrenched to manufacturer specs—under-tightened bolts invite arcing; over-tightened ones crush terminals.
What Tools Are Needed for Shunt Calibration?
Calibration is a symphony of tools. A metrology-grade digital multimeter (DMM) with 6.5-digit resolution captures microvolt drops. A precision current source—stable to ±10 ppm—feeds known currents, while thermal chambers simulate operating extremes. Don’t forget a null detector for Wheatstone bridge setups or a shunt calibrator with NIST-traceable certification. For field work, infrared thermometers spot hotspots, and micro-ohm meters validate connections. Pro tip: Use superconducting shorts to zero out lead resistance—because even a milliohm of stray impedance can corrupt readings.
How to Verify a Shunt’s Accuracy After Installation?
Post-installation, stress-test the shunt under real-world loads. Inject a calibrated current (e.g., 80% of rated capacity) and measure the voltage drop across its terminals. Compare against the shunt’s specified resistance (R = V/I) using a DMM with guarded inputs to block EMI. For high-stakes applications, perform a delta calibration: measure at 20%, 50%, and 100% load to map linearity errors. Check for thermal drift by cycling ambient temperatures while monitoring TCR-induced deviations. Finally, log baseline data—future diagnostics depend on this fingerprint.
How Do DC Shunts Compare to Hall Effect Sensors in Current Measurement?
DC shunts and Hall effect sensors are rival titans in current measurement, each governed by distinct physics. Shunts rely on resistive principles, slicing through current via Ohm’s Law, while Hall sensors harness magnetic field perturbations caused by current flow. Shunts excel in direct, analog precision; Hall sensors thrive in isolated, contactless environments. The battleground? Applications demanding either microvolt-level fidelity or galvanic separation.
What Are the Pros and Cons of Each Method?
DC Shunts:
Pros: Unmatched linearity (±0.1% or better), passive operation (no external power), and low cost for high-current DC systems.
Cons: Intrinsic power loss (I²R heating), no galvanic isolation, and sensitivity to temperature drift.
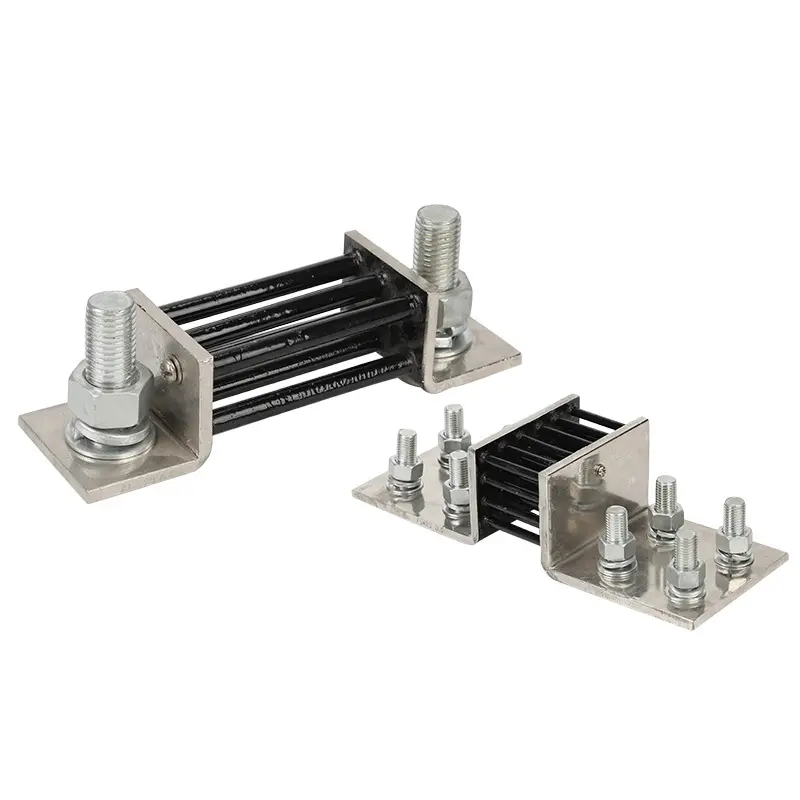
Hall Effect Sensors:
Pros: Isolation from high voltages, AC/DC compatibility, and minimal insertion loss.
Cons: Nonlinearity (±1% typical), susceptibility to stray magnetic fields, and dependency on stable power supplies.
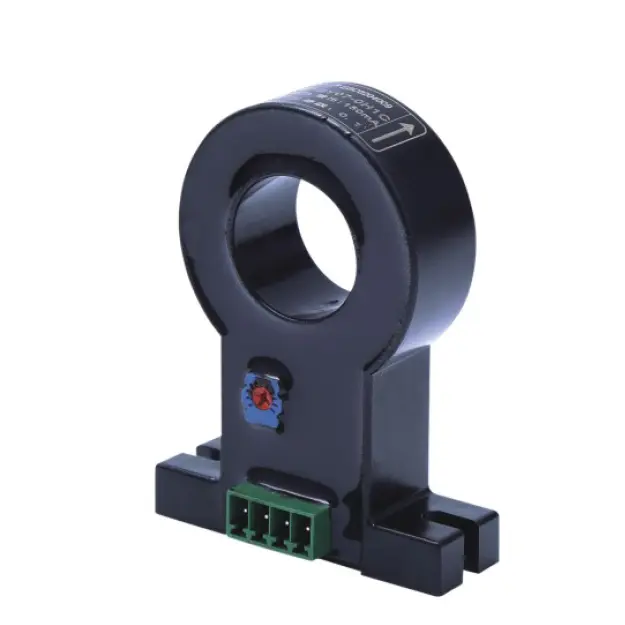
When Is a Shunt a Better Choice Than a Hall Sensor?
Choose shunts when accuracy is non-negotiable—think laboratory-grade power supplies, EV battery monitoring, or precision welding controls. They dominate in DC environments where isolation isn’t critical, and budgets demand simplicity. Shunts also outmuscle Hall sensors in high-frequency noise environments (e.g., motor drives), where magnetic interference would swamp Hall outputs.
How Do Costs and Complexities Differ Between the Two?
Shunts win the frugality crown: a 500A manganin shunt costs ~50,whileacomparableHallsensormoduleruns50,whileacomparableHallsensormoduleruns200+. But hidden costs lurk. Shunts demand precision amplifiers and Kelvin connections, adding circuit complexity. Hall sensors simplify installation (clip-around designs) but require signal conditioning and temperature compensation. For ultra-high currents (>1kA), shunts remain unbeatable—scaling Hall sensors to kiloampere ranges balloons costs exponentially.
Conclusion: Why Understanding DC Shunts Matters
Key Takeaways: The Silent Backbone of Precision
DC shunts are the unsung heroes of electrical metrology—engineered alloys that transform raw current into actionable data. From their manganin cores to Kelvin connections, every design choice serves accuracy. Whether monitoring EV battery arrays or stabilizing microgrids, shunts thrive where milliohms and microvolts dictate success.
Choosing the Right Shunt: A Decision That Electrifies Reliability
Selecting a shunt isn’t just about specs; it’s about syncing physics with application. A mismatched shunt risks thermal runaway in solar inverters or cripples lab-grade instruments with drift. Prioritize TCR ratings for volatile environments, current density for industrial loads, and isolation needs for safety-critical systems. The right shunt isn’t a component—it’s insurance.
When in Doubt, Lean on Expertise
Even seasoned engineers face shunt dilemmas: Is manganin worth the premium over constantan? Can a shunt survive salt spray in offshore rigs? Don’t gamble—consult metrologists or manufacturers. Firms like Isabellenhütte or Ohio Semitronics offer application-specific guidance, ensuring your shunt isn’t just adequate but optimized.