In the demanding world of industrial welding, environments can vary drastically, each with its own set of challenges. From offshore oil platforms hit by relentless salt spray to mining equipment working in dust-heavy tunnels, and from freezing arctic pipelines to scorching desert solar fields, welding equipment must perform flawlessly. The key to ensuring reliable welding under these extreme conditions? High-quality DC shunts, which provide the precise current measurement necessary to produce consistent, high-quality welds no matter how harsh the environment.
The Unique Challenges of Extreme Environment Welding
Welding in extreme environments is a complex challenge. What’s the real story here? Standard equipment simply doesn’t cut it when exposed to these harsh conditions. To fully understand the demands, we need to explore the specific challenges welding systems face in these environments.
High Temperature Environments
Welding in high-temperature environments introduces unique challenges for equipment durability and performance. Ready for the good part? Welding operations in extreme heat require equipment that can maintain accuracy and functionality despite elevated temperatures. Here’s what’s at stake:
- Thermal loading: Welding equipment often operates under heat stress from both external and internal sources. The equipment has to manage the added thermal load effectively.
- Cooling limitations: In high-temperature environments, the natural heat dissipation mechanisms are less effective, which accelerates wear and tear on components.
- Material property changes: The electrical characteristics of components can change with temperature, leading to inaccuracies in current measurement if not properly managed.
- Accelerated aging: Heat speeds up the degradation of materials, increasing the likelihood of failure over time.
- Thermal cycling: Extreme temperature variations—common in many harsh environments—cause repeated expansion and contraction, adding mechanical stress to the system.
These conditions are a standard part of environments like desert solar fields, steel mill maintenance, and oil refinery construction, where temperatures routinely exceed 50°C (122°F).
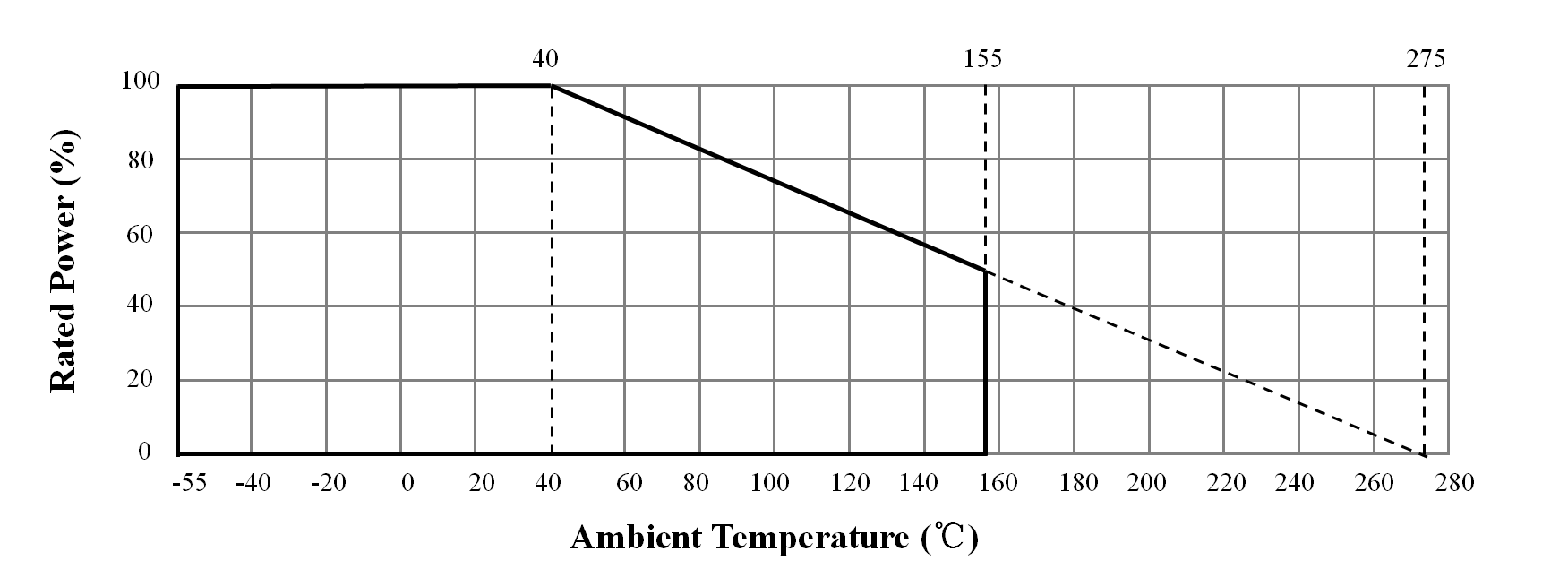
High Humidity and Corrosive Environments
Humidity and corrosive elements pose another set of threats to welding equipment. But here’s the kicker: moisture and chemical exposure can quickly degrade even the most robust systems. Key challenges include:
- Corrosion acceleration: Saltwater, chemicals, and moisture in the air cause rapid degradation of metal components.
- Insulation degradation: Moisture can penetrate insulation, leading to potential electrical shorts or failures.
- Connection resistance: Corrosion at electrical connections increases resistance and generates excess heat, which further degrades the components.
- Short-circuit risk: Condensation in high-humidity environments creates the potential for current leakage, posing significant safety risks.
- Accelerated oxidation: Components exposed to moisture and salt can oxidize much faster than in dry environments.
Offshore platforms, shipyards, and chemical plants are examples of locations where equipment is frequently exposed to 100% humidity, salt spray, and corrosive chemicals, requiring special measures to prevent premature failure.
Vibration and Mechanical Shock
Industrial environments often subject equipment to constant mechanical stress, from vibrations to shocks. What’s the real story here? This physical strain can seriously affect the performance of welding systems, especially if not properly mitigated. Here are the key mechanical challenges:
- Connection loosening: Vibrations can gradually loosen electrical connections, leading to unstable performance and potential failures.
- Component fatigue: Repeated mechanical stress can cause material fatigue, weakening components and leading to premature failure.
- Alignment shifts: Constant vibrations can alter the positioning of critical components, disrupting precision measurements and operations.
- Intermittent connections: Mechanical stress can cause brief interruptions in connections, leading to unstable current readings and inconsistent weld quality.
- Structural damage: In extreme cases, severe impacts or shocks can physically damage components, completely halting welding operations.
Mining equipment, shipbuilding, and heavy-duty construction applications all experience these stresses, which require welding equipment that can withstand continuous vibration and occasional shocks.
Electromagnetic Interference Environments
In many industrial settings, electromagnetic interference (EMI) can be a major issue. What’s the kicker? The presence of strong electrical fields or large electrical systems can corrupt signal integrity, making it challenging to maintain reliable welding control. Here are the challenges posed by EMI:
- Signal corruption: External electromagnetic fields can induce noise in the measurement circuits, leading to incorrect readings.
- Data inaccuracy: Noise interference can lead to errors in current measurements, which disrupt the welding process.
- Control instability: Corrupted signals can trigger incorrect adjustments in welding parameters, leading to poor weld quality.
- Communication errors: EMI can interfere with data transmission between system components, causing synchronization issues.
- Calibration drift: Persistent electromagnetic interference can cause the system to drift out of calibration, resulting in long-term inaccuracies.
These issues are particularly common in automotive manufacturing, shipyards, and large fabrication plants where multiple welding stations, large motors, or induction heating equipment operate in close proximity.
Summary Table: Challenges in Extreme Environment Welding
Environmental Factor | Challenge | Impact on Welding Systems |
---|---|---|
High Temperature | Thermal stress, heat dissipation limitations | Accelerated equipment degradation |
High Humidity | Corrosion, insulation degradation, short-circuit risk | Increased risk of failure |
Vibration/Shock | Loosening connections, fatigue, alignment shifts | Inconsistent welding quality |
Electromagnetic Interference | Signal corruption, data inaccuracies | Control instability, welding defects |
DC Shunt Design Features for Environmental Resilience
High-quality DC shunts designed for use in extreme environments incorporate several key features that ensure their reliable performance. Ready for the good part? The resilience of a DC shunt is largely determined by the materials used and how the device is constructed. Let’s take a closer look at the features that make DC shunts so effective in harsh conditions.
Material Selection and Durability
The materials used in DC shunts directly influence their ability to perform under challenging environmental conditions. What’s the real story? Choosing the right materials ensures longevity and performance. Here are the key material considerations:
- Manganin alloy: Premium DC shunts use manganin (a copper-manganese-nickel alloy), known for its excellent temperature stability and low thermal electromotive force (EMF), which makes it ideal for high-precision measurements.
- Corrosion-resistant terminals: DC shunts with corrosion-resistant terminals and appropriate plating help resist the harmful effects of moisture and chemicals in the environment.
- Robust insulation: High-quality insulation materials ensure that the shunt maintains its integrity even in wet, dusty, or chemically corrosive conditions.
- Thermal matching: Materials with compatible thermal expansion coefficients help prevent mechanical stress during temperature cycles, ensuring stable performance over time.
- Vibration-resistant construction: The shunt’s design should minimize susceptibility to mechanical stress and vibration, ensuring longevity and reliability in harsh environments.
The FL-19 series shunts are an example of shunts designed with these materials and features, ensuring optimal performance even in extreme conditions.
Sealing and Protection Measures
When it comes to ensuring long-term reliability in extreme environments, sealing and protection are critical. But here’s the kicker: without proper protection, even the best materials can fail. Key protective measures include:
- Encapsulation options: Protective coatings or encapsulation can shield DC shunts from environmental contaminants, including dust, moisture, and chemicals.
- Moisture resistance: Special treatments prevent moisture ingress, helping to maintain functionality in wet environments.
- Chemical resistance: High-quality materials withstand exposure to oils, fuels, and industrial chemicals, which are common in manufacturing plants and offshore platforms.
- Particle exclusion: Designs that minimize the accumulation of dust and particulates ensure that the shunt’s performance isn’t compromised.
- UV stability: UV-resistant materials protect the shunt from the harmful effects of prolonged sun exposure, which is critical for outdoor applications like solar fields.
These protective features ensure that the DC shunt can continue to provide accurate measurements despite the environmental challenges it faces.
Temperature Compensation Mechanisms
Temperature fluctuations can cause measurement errors, but high-quality DC shunts incorporate several mechanisms to compensate for these effects. Ready for the good part? Here’s how they maintain measurement accuracy:
- Low temperature coefficient materials: Shunts with low temperature coefficients (typically below 25ppm/°C) ensure that resistance changes due to temperature variations are minimal.
- Thermal design: Optimized heat dissipation helps minimize temperature rise in high-temperature environments, ensuring stable performance.
- Balanced construction: DC shunts are designed to minimize thermal gradients, ensuring uniform temperature distribution across components.
- Thermal isolation: Features that protect sensitive elements from external heat sources help maintain accuracy in fluctuating temperature conditions.
- Temperature monitoring: Some DC shunts include temperature sensing options, allowing for dynamic compensation based on real-time temperature data.
These features ensure that welding equipment can operate reliably even in environments where temperatures fluctuate widely or consistently remain high or low.
Summary Table: DC Shunt Features for Environmental Resilience
Feature | 效益 | Application Impact |
---|---|---|
Manganin Alloy | Excellent temperature stability and low thermal EMF | Ensures precision in extreme temperatures |
Corrosion-Resistant Terminals | Resists environmental damage | Ensures longevity in harsh environments |
Robust Insulation | Maintains integrity in wet or chemically harsh environments | Enhances reliability in corrosive conditions |
Vibration-Resistant Design | Minimizes mechanical stress | Ensures stable operation in vibrating environments |
Encapsulation | Protects against contaminants | Ensures performance in dust and moisture-rich environments |
Special Applications Case Analysis
The value of environmentally resilient DC shunts is best illustrated through specific applications in extreme environments. Ready for the good part? Let’s take a look at real-world examples of how these shunts have been successfully deployed.
Marine Engineering Welding
Offshore and marine environments present some of the most challenging conditions for welding equipment. What’s the kicker? Salt spray, constant humidity, and platform movement make reliability absolutely critical. Here’s how DC shunts can make a difference:
- Environmental conditions: Salt spray, 100% humidity, constant motion, and temperature cycling all put welding equipment to the test.
- Application requirements: High reliability, minimal maintenance, and consistent performance are essential for maintaining safety and productivity.
- Consequences of failure: Equipment failure leads to costly downtime, difficult repairs, and potential safety hazards.
In a shipyard using FL-19 series DC shunts, the company reported a 94% reduction in measurement-related failures compared to previous equipment. The corrosion-resistant construction and stable performance despite temperature and humidity changes were cited as the primary reasons for this improvement.
Mining Equipment Manufacturing
Mining equipment operates in extremely harsh conditions, facing dust, vibration, and a wide range of temperatures. What’s the real story? DC shunts designed for durability are essential for ensuring consistent weld quality in such challenging environments. Key aspects include:
- Environmental conditions: Dust, vibration, impact, and wide temperature variations all create significant challenges.
- Application requirements: Durability, resistance to mechanical stress, and minimal maintenance are critical.
- Consequences of failure: Production delays, poor weld quality, and field failures are common risks.
A mining equipment manufacturer upgraded their welding systems with high-durability DC shunts and saw an 87% reduction in current measurement issues, significantly improving weld consistency for high-stress components.
Polar Environment Construction
In polar environments, such as arctic and antarctic construction projects, extreme cold and rapid temperature changes create a unique set of challenges. But here’s the kicker: DC shunts that can perform in subzero temperatures are essential for these operations. Here’s why:
- Environmental conditions: Temperatures often drop below -40°C, with rapid warming during welding and condensation during storage.
- Application requirements: Cold-start capability, stability in fluctuating temperatures, and resistance to moisture are crucial for maintaining reliable operation.
- Consequences of failure: Delays in production, limited repair options, and costly shutdowns are common in these extreme conditions.
In northern Canada, a pipeline construction project utilized specially selected DC shunts designed for extreme temperatures. Despite daily temperature swings of over 30°C, the systems maintained calibration and allowed for continuous production, saving the company an estimated $350,000 per day.
Summary Table: Special Application Case Analysis
Application Type | Environmental Challenges | Results |
---|---|---|
Marine Engineering | Salt spray, humidity, platform motion | 94% reduction in measurement failures |
Mining Equipment | Dust, vibration, extreme temperatures | 87% reduction in current measurement issues |
Polar Construction | Subzero temperatures, rapid warming, condensation | Continuous production despite extreme cold |
Performance Verification and Testing Methods
Ensuring that DC shunts will perform reliably in extreme environments requires thorough testing. Ready for the good part? Here’s how manufacturers can verify the performance of their shunts in real-world conditions.
Environmental Simulation Testing
To ensure reliable performance, DC shunts undergo rigorous environmental simulation testing. These tests mimic the stressors the equipment will face in the field:
- Temperature cycling: Tests across the full operating temperature range.
- Humidity exposure: Exposure to high-humidity chambers to simulate extreme moisture conditions.
- Salt spray testing: Accelerated corrosion testing to simulate marine environments.
- Vibration testing: Mechanical stress evaluation on shake tables to simulate operating environments with high vibration.
- Combined stress testing: Simultaneous exposure to multiple environmental factors to evaluate overall performance.
These tests ensure that DC shunts can maintain accuracy and reliability, no matter what environment they are exposed to.
Accelerated Aging Trials
To predict long-term performance, accelerated aging tests subject DC shunts to harsher conditions than they would typically encounter:
- Elevated temperature aging: Higher temperatures speed up thermal degradation, mimicking years of use.
- Thermal cycling: Repeated temperature changes induce stress and simulate long-term exposure to temperature extremes.
- Power cycling: Alternating between full load and no load to create thermal stress.
- Corrosive atmosphere exposure: Exposing shunts to concentrated chemicals to simulate extreme environments like oil platforms and chemical plants.
These accelerated tests provide confidence in the long-term reliability of DC shunts without having to wait for years of field experience.
Field Validation Approaches
Real-world testing helps confirm the reliability of DC shunts under operational conditions:
- Pilot installations: Limited deployments in actual operating environments to validate performance.
- Comparative monitoring: Side-by-side testing with reference equipment to ensure consistent results.
- Long-term data collection: Monitoring performance over extended periods in the field.
- Post-exposure analysis: Examining components after extended use in harsh conditions to assess durability.
- Customer feedback programs: Gathering real-world data from users to assess system reliability.
These field validation methods confirm that laboratory results translate to real-world reliability.
Summary Table: Testing and Validation Methods
Testing Method | 說明 | 效益 |
---|---|---|
Environmental Simulation | Testing under controlled harsh conditions | Verifies reliability in real-world environments |
Accelerated Aging | Simulating years of use under extreme conditions | Predicts long-term performance |
Field Validation | Real-world testing to confirm laboratory results | Ensures accuracy and reliability under operational stress |
Implementation Best Practices
Implementing DC shunts in extreme environments requires careful planning. Let’s explore the best practices to ensure reliable operation.
Installation Guidelines for Harsh Conditions
Proper installation is key to maintaining the longevity and performance of DC shunts. Ready for the good part? These best practices will help you get it right:
- Use appropriate mounting methods: Secure the shunt in a way that accommodates thermal expansion and vibration.
- Implement proper connection techniques: Ensure connections are secure and can withstand environmental stress.
- Apply protective measures: Use additional sealing or enclosures for environments with high dust or moisture.
- Consider thermal management: Heat sinks or cooling systems can help manage high temperatures in extreme environments.
- Provide strain relief: Manage cables to prevent stress on connections, which could lead to failures.
Following these guidelines ensures that the DC shunts perform optimally even in the harshest environments.
Maintenance and Inspection Protocols
Maintenance is essential for ensuring reliable performance in extreme conditions. But here’s the kicker: regular maintenance is the key to keeping systems running smoothly in these environments. Consider the following best practices:
- Establish inspection schedules: Regular checks for signs of wear or environmental damage can help identify issues before they cause failures.
- Implement cleaning procedures: Use proper methods to remove contaminants such as dust, salt, or chemicals.
- Verify connections: Regularly test the integrity of electrical connections to prevent failures due to corrosion or loosening.
- Conduct performance verification: Periodically check the accuracy of the shunt against reference standards.
- Document environmental exposure: Track extreme conditions the shunt has been exposed to for better understanding of potential long-term effects.
Proper maintenance ensures the DC shunt continues to deliver accurate measurements in the long run.
Backup and Redundancy Considerations
In extreme environments, redundancy is essential for ensuring continued operation. Ready for the good part? Here’s how to minimize the impact of a failure:
- Dual measurement systems: Using parallel DC shunts to monitor the same welding process.
- Backup power sources: Ensure the welding system continues to function during power fluctuations.
- Alternative verification methods: Use secondary systems to verify current measurements if the primary shunt fails.
- Spare components: Keep spare parts on hand for quick replacements in the field.
- Failure mode planning: Establish clear procedures for addressing failures to minimize downtime.
These redundancy measures ensure that if one system fails, others will step in to keep the operation going smoothly.
Summary Table: Implementation Best Practices
最佳實務 | 說明 | 效益 |
---|---|---|
Proper Mounting | Ensure the shunt is securely mounted to withstand vibration and thermal expansion | Prevents physical damage |
Protective Measures | Implement sealing and enclosures for harsh environments | Protects against contaminants |
Maintenance | Regular inspections and testing of connections | Ensures long-term reliability |
備援 | Backup systems and spare components | Minimizes downtime during failures |
Real-World Success Stories
The true value of environmentally resilient DC shunts shines through in real-world applications. What’s the kicker here? Let’s look at how these shunts perform in different industries:
Offshore Platform Welding Systems
An offshore oil platform in the North Sea implemented welding systems with FL-19 series DC shunts:
- Challenges: Salt spray, constant humidity, platform movement, and limited access for maintenance.
- Results: Zero measurement-related failures over three years compared to quarterly failures with previous equipment.
- Economic Impact: The system saved $1.2 million in lost production time by eliminating delays due to equipment failure.
The platform manager noted that “the reliability of current measurement has
transformed our maintenance approach from reactive to predictive, eliminating a major source of production interruptions.”
Desert Solar Field Construction
In the Southwestern United States, a solar field construction project faced extreme heat and dust:
- Challenges: Temperatures exceeding 45°C and abrasive dust.
- Results: Consistent welding quality with measurement drift under 0.2%.
- Economic Impact: The project finished two weeks ahead of schedule due to fewer equipment issues.
The project manager commented that “in conditions where standard equipment would fail daily, our enhanced systems performed flawlessly, allowing continuous production through even the hottest days.”
Arctic Pipeline Welding
A pipeline project in northern Alaska faced extreme cold:
- Challenges: Temperatures below -40°C and rapid warming during welding.
- Results: Successful operation at -48°C with consistent weld quality.
- Economic Impact: Saved $350,000 per day in crew and equipment costs by keeping production on schedule.
The welding supervisor remarked, “The ability to maintain precise current control despite the extreme cold was the difference between meeting our schedule and facing costly delays.”
Summary Table: Real-World Success Stories
Application Type | Environmental Challenges | Results |
---|---|---|
Offshore Platform | Salt spray, humidity, platform movement | Zero failures in 3 years, $1.2 million savings |
Desert Solar Field | Heat, dust | 0.2% drift, project ahead of schedule |
Arctic Pipeline | Extreme cold, rapid temperature changes | Consistent quality, $350,000 daily savings |
Conclusion: Reliability When It Matters Most
In extreme environments, equipment reliability is crucial. For welding systems exposed to temperature extremes, corrosive atmospheres, and mechanical stress, high-quality DC shunts provide the foundation for consistent, high-quality performance. By ensuring accurate current measurements, DC shunts make reliable welding possible in some of the toughest conditions on earth.
For manufacturers, integrating these resilient components into welding equipment offers a clear competitive edge. In industries that demand unwavering performance, incorporating environmentally resilient DC shunts ensures a reliable, cost-effective solution.
常見問題部分
Q1: What environmental challenges do DC shunts face in extreme conditions?
A1: DC shunts must endure high temperatures, humidity, vibration, and corrosion, which can compromise performance if not properly designed.
Q2: How do DC shunts maintain accuracy in fluctuating temperatures?
A2: High-quality DC shunts use low-temperature coefficient materials and thermal designs to ensure stable measurements despite temperature changes.
Q3: Why is corrosion resistance important for DC shunts in marine environments?
A3: In marine environments, salt spray and humidity can accelerate corrosion, which affects the performance and lifespan of electrical components. Corrosion-resistant DC shunts prevent this issue.
Q4: How does vibration affect DC shunts in industrial environments?
A4: Vibration can loosen connections and cause alignment shifts, leading to inaccurate measurements. Vibration-resistant DC shunts ensure stable performance despite mechanical stress.
Q5: How are DC shunts tested for reliability in extreme environments?
A5: DC shunts undergo environmental simulation testing, accelerated aging trials, and field validation to ensure they perform reliably under real-world conditions.

